Entraînement rapide, inspection pointue
Manipulation et inspection des défauts de plaquettes amovibles.
en.ids-imaging.com
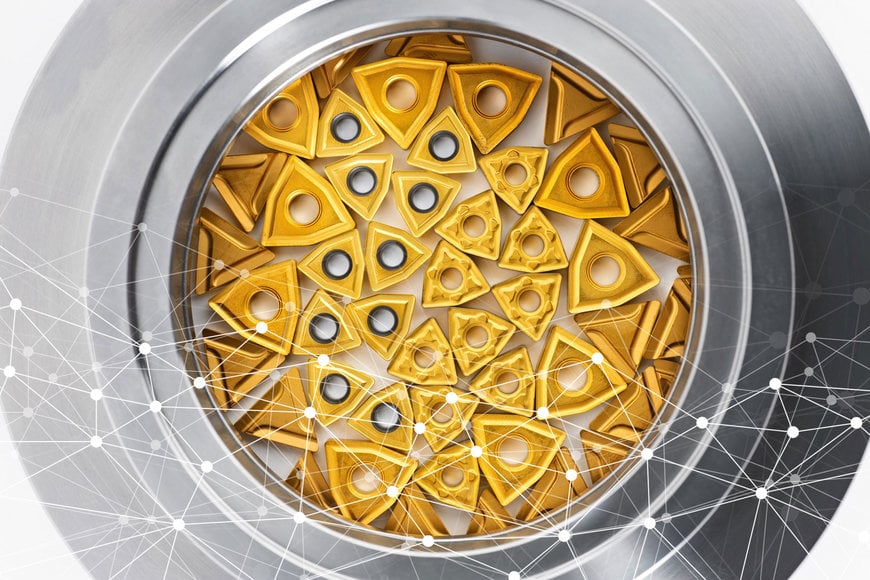
Les plaquettes amovibles sont des outils de coupe interchangeables, indispensables dans diverses applications industrielles, notamment dans le traitement des métaux. Ils servent de support de coupe pour l'usinage des métaux, des matières plastiques ou du bois. Leur fabrication nécessite des procédés de fabrication de haute précision afin de garantir une géométrie exacte et une finition irréprochable. Même des écarts minimes affectent non seulement la durée de vie, mais aussi les performances de la plaquette. Les plus petits défauts, invisibles à l'œil nu, peuvent causer d'immenses dommages, par exemple lors du fraisage ou de la découpe de pièces de grande valeur - engendrant des frais supplémentaires. Pour s'assurer que seules des plaquettes sans défaut quittent le processus de production et répondent aux strictes exigences en matière de durabilité et de fiabilité, un contrôle qualité minutieux est indispensable. Un projet phare de Xactools, spécialiste de l'automatisation et de la métrologie dans le Bade-Wurtemberg, montre comment l'intelligence artificielle peut aider l'inspection visuelle à faire des bonds en avant. Pour un fabricant mondial de plaquettes amovibles basé en Scandinavie, la PME souabe a développé un système de manutention et d'inspection entièrement automatisé, dans lequel la solution DENKnet joue un rôle décisif dans l'analyse d'images basée sur l'IA et établit de nouveaux critères en termes de performance, de production zéro défaut et de vitesse.
Application
Environ 1,2 million de plaquettes amovibles quittent chaque semaine les ateliers de production des Scandinaves, qui doivent garantir une sécurité maximale des processus et une productivité au maximum, par exemple dans l’industrie de la métallurgie, l'industrie automobile ou l'industrie aérospatiale.
La fabrication s'effectue par un processus de frittage, au cours duquel des métaux en poudre, des métaux durs et d'autres matériaux sont comprimés dans la forme souhaitée, puis frittés, c'est-à-dire liés entre eux par la chaleur et la pression. La structure solide et robuste ainsi obtenue permet de combiner des matériaux aux propriétés différentes afin d'obtenir les caractéristiques de coupe et de résistance à l'usure souhaitées. Après le processus de frittage, les rebords des plaquettes sont arrondis et poncés, leurs surfaces grenaillées, poncées et enduites.
Le système Robotvision des ingénieurs souabes intervient alors directement après la deuxième étape de fabrication, le processus de frittage. "Plus les défauts sont détectés tôt dans le processus, plus la réparation est efficace et peu coûteuse", explique Marvin Krebs, directeur des ventes techniques chez Xactools, pour justifier la position du système. Pour la manipulation et l'inspection des défauts des plaquettes amovibles, huit caméras industrielles à haute résolution et deux robots Spider sont utilisés, qui jettent un œil sur trois nids de plateaux tounands et autant de palettes à broches et qui les équipent. L'IA de DENKnet constitue le cœur du système complexe de traitement d'images entre les caméras, les robots et un rack de calcul multi-GPU.
Exigences
Les domaines d'application des petites pièces d'outillage sont aussi variés que leur consistance et leurs géométries. Ce fabricant dispose à lui seul d'un portefeuille d'environ 2800 produits, répartis en près d'une centaine de familles de géométries. Pour tous ces produits, le but était d'automatiser la manutention et l'inspection des défauts. "Le premier défi résulte des nombreuses variations de couleur de la poudre lors du processus de pressage", explique Marvin Krebs. "Si certains paramètres comme le temps, l'impression ou le positionnement varient, cela entraîne des variations de couleur ou de brillance, ou encore une répartition différente de ce que l'on appelle les speckles sur la surface, ce qui n'est pas un défaut". Le logiciel utilisé d'évaluation d'images basé sur l'IA a dû être entraîné de manière à reconnaître correctement les nombreuses variations de couleur possibles des surfaces et à les évaluer comme étant "OK". D'autre part, les moindres irrégularités telles que les fissures, les rayures, les inclusions ou autres anomalies doivent être reconnues comme telles et classées comme "NOK". L'examen des surfaces métalliques est considéré comme l’art suprême de l'inspection de surfaces, car celles-ci peuvent être mates, brillantes ou même réfléchissantes. "Pour cette application, l'IA a dû être extrêmement attentive aux variations et aux conditions d'éclairage", souligne Marvin Krebs.
L'IA reconnaît le contour des plaquettes et fait la différence entre OK et NOK, même pour les nouvelles pièces.
Mais au-delà de l'aspect visuel, c'est aussi la géométrie des plaquettes qui est en jeu. Des catégories telles que le triangle, le rectangle, le losange ou le carré se déclinent dans d'innombrables variantes en raison d'infimes variations et sont donc divisées en sous-catégories appelées familles de géométrie. Pour l'entraînement des réseaux, Xactools a effectué une présélection, près d'une centaine de familles de géométries ont été définies puis entraînées par le fabricant lui-même. Ce qui semble être une tâche laborieuse a été réalisé très rapidement.
"Pour chaque famille de géométrie, pas plus de 20 à 30 images ont été nécessaires pour l'apprentissage", se souvient Marvin Krebs. L'IA de palettisation DENKnet utilisée à cet effet utilise le réseau de segmentation et de classification DENKnet. Le client n'a eu besoin que de xx heures environ pour se former à cette solution d'analyse d'image personnalisée avec le DENK VISION AI Hub. En quelques mois, l'IA a été intégrée dans la ligne de production et a obtenu dès le début des résultats d'IA fiables et quasiment parfaits pour les composants métalliques à contrôler. "Les plaquettes identifiées comme défectueuses sont triées et regroupées en fonction de la taille et de la position du défaut.
L'analyse d'images par l’IA détecte alors plus de 99 pour cent des erreurs de fabrication", ajoute Daniel Routschka, Sales Manager Artificial Intelligence chez IDS Imaging Development Systems.
Mais comment le système fonctionne-t-il exactement ?
Au total, huit caméras d'une résolution comprise entre 5 et 30 mégapixels fournissent des images en direct des plaquettes amovibles, qui sont respectivement mises en position par des préhenseurs magnétiques ou interchangeables. Par exemple, deux caméras saisissent les différentes plaquettes amovibles, l’une par le bas et l’autre par le haut afin de contrôler les défauts de surface. Deux autres caméras contrôlent les bord coupants. Un écran mobile de 1 x 1 mètre assure un éclairage extrêmement élevé au niveau des palettisations. "Le système détecte des défauts de l'ordre du millième de millimètre", souligne Marvin Krebs. Cela permet de garantir qu'aucun dommage ne sera causé aux surfaces haut de gamme qui seront traitées ultérieurement. Car "des processus de fraisage irréguliers et défectueux peuvent éventuellement nuire à la rentabilité et à la compétitivité", explique le fabricant.
Afin d'éviter cela dès le processus de fabrication et de faire preuve de la plus grande prudence possible, le système prend également des photos du contour et de la position des plaquettes après l'inspection des surfaces et des bords.
Détection des contours par le bas après le prélèvement sur le Crucible et avant la dépose sur le premier nid de la table tournante.
Il voit exactement où et dans quelle position de rotation se trouve la plaquette, afin que le préhenseur magnétique puisse finalement la placer sur des palettes à broches. Pour s'en assurer, le préhenseur auquel adhère la plaquette passe au-dessus d'une caméra qui détecte par le dessous la position exacte du trou. En même temps, le contour de la plaquette et le bord extérieur du préhenseur sont détectés afin de corriger, si nécessaire, la position de la plaquette et de viser la broche avec précision. En outre, la position de chaque broche est détectée afin d'identifier les broches tordues et cassées, de sorte que la palettisation ne soit pas effectuée sur celles-ci.
L'analyse d'image IA détecte les trous et donc le centre de la pièce pour la prise avec un préhenseur magnétique ou interne.
"L'installation fonctionne depuis six mois, et entre-temps, l'IA globale à apprentissage automatique reconnaît des pièces qu'elle n'avait jamais vues auparavant. Au bout de trois à quatre mois, il n'était déjà plus nécessaire de procéder à un nouvel entraînement pour inspecter les nouvelles variantes de plaquettes. Pour l'IA, la géométrie sous-jacente n'a plus d'importance, elle connaît le contour et peut également faire la différence entre OK et NOK pour les nouvelles pièces", explique Marvin Krebs.
Analyse d'image par IA de haute performance avec 99% d'efficacité de picking
Pour Marvin Krebs, la valeur ajoutée du système DENKnet par rapport au traitement d'image traditionnel est évidente : "Sans l'IA, la création des familles de pièces et la détection des défauts seraient totalement impensables. Avec un traitement d'image basé sur des règles, le robot reconnaîtrait des pièces situées dans la norme comme NOK et les éliminerait". De plus, grâce au Vision AI Hub, aucun codage en dur n'est nécessaire et la flexibilité des réseaux a été un autre critère de sélection pour le logiciel intelligent DENKnet. "Nous avons pu facilement intégrer l'IA de palettisation DENKnet et plusieurs classes d'objets pour les défauts dans notre propre logiciel de traitement d'images Xactools par le biais d’une API", explique Marvin Krebs.
Mais ce qui est quasiment unique, c'est la performance de la solution. L'ensemble du processus d'inspection se déroule en un temps de cycle de quatre secondes, avec une efficacité de picking de presque 100 %. Une énorme puissance de calcul est nécessaire pour analyser les images en direct issues de huit caméras via une DLL (Dynamic Link Library).
"Ce n'est pas sans raison que nous travaillons avec DENKnet. La performance n'est pas comparable à celle d'autres fournisseurs, elle est vraiment excellente", souligne Marvin Krebs. "Utiliser l'intelligence artificielle dans ses différentes variantes à une telle échelle, cela n'a jamais été fait auparavant". Actuellement, d'autres variations sont testées, par exemple pour simplifier encore la détection des trous.
Reconnaissance du centre de la pièce par le bas pour corriger la position avant de la déposer sur la palette de broches
Perspectives
Les surfaces et géométries extrêmement variées ainsi que les intolérances de l'ordre du millième de millimètre font de l'inspection visuelle des plaquettes amovibles une discipline reine qui peut être appliquée à de nombreuses autres applications exigeantes. L'environnement d'entraînement auto-explicatif de la solution DENKnet sert ici d'outil incomparablement simple et performant à la fois, car il peut être utilisé sans connaissances en programmation et permet l'entraînement automatisé de l'IA en quelques clics. Pour cela, les technologies les plus diverses sont disponibles dans le domaine de la vision artificielle. "Comme notre solution peut être adaptée à chaque cas d'application et qu'il n'y a pas de limites - quel que soit le nombre de "classes", la technologie de caméra, la taille des images ou même le mélange de fichiers de données, par exemple en termes de résolution et de type - des solutions peuvent être créées dans n'importe quel domaine", explique Daniel Routschka, Sales Manager Artificial Intelligence chez IDS Imaging Development Systems.
"Plus de 95% de nos installations de mesure et de contrôle ont au moins une classe d'objets IA intégrée. Les domaines d'application possibles sont de plus en plus vastes pour nous, le marché est en pleine croissance", confirme Marvin Krebs. Des perspectives prometteuses pour cette formation automatisée exemplaire en matière d'IA, qui répond aux exigences les plus élevées.
www.ids-imaging.fr
This email address is being protected from spambots. You need JavaScript enabled to view it.