electronique-news.com
15
'21
Written on Modified on
Que peut apporter la 5G à l’automatisation industrielle ?
La connectivité est un élément essentiel de l’industrie 4.0. En effet, l’échange de données entre le site de production, l’edge et le cloud permet de convertir les actifs industriels en systèmes cyberphysiques.
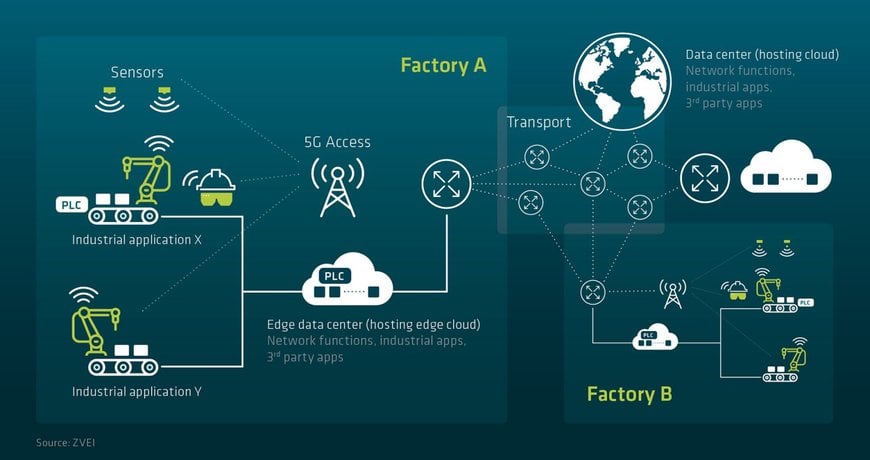
La connectivité sans fil est un principe intéressant pour les propriétaires et exploitants d’usines qui offre de nombreux avantages. Notamment une plus grande flexibilité pour réaménager et réorganiser des équipements sur un site de fabrication, mais aussi la possibilité de connecter des actifs auparavant inatteignables ou d’étendre la capacité en ajoutant des équipements sans que cela ne nécessite d’établir un planning compliqué ou de procéder à un coûteux recâblage. De plus, les normes sans fil supportant la mobilité permettent désormais d’intégrer de nouveaux types d’équipements connectés aux systèmes de gestion d’usine, par exemple des véhicules autonomes.
Il existe toute une variété de normes et protocoles sans fil utilisés pour diverses applications. Cela va du simple dispositif E/S sans fil utilisé pour connecter de petits groupes de capteurs difficiles d’accès ou fixés sur des pièces mobiles aux grands réseaux de capteurs sans fil (RCSF) distribués, en passant par les systèmes d’automatisation d’usine et de processus. Malgré les nombreux avantages qu’elles apportent, chacune de ces technologies présente aussi ses inconvénients.
Des réseaux filaires aux réseaux sans fil, l’industrie fait sa transition
Le Bluetooth® est une technologie bien connue, simple d’utilisation et qui permet de réaliser des économies d’échelle sur des applications industrielles.
Si le Bluetooth doit sa notoriété à ses applications de mise en réseau grand public, des caractéristiques telles que l’étalement de spectre par saut de fréquence (FHSS) et des fonctions de sécurité intégrées comme le chiffrement et l’authentification répondent aux exigences industrielles en matière de coexistence, de sécurité et de protection contre le piratage. Cette technologie procure aux adaptateurs de ports Ethernet un moyen fiable d’échanger des données de contrôle à l’aide d’un protocole tel que PROFINET. Grâce au Bluetooth, les gestionnaires peuvent appliquer facilement des mises à jour de micrologiciel à leurs équipements sans qu’il leur soit besoin de connecter un câble, simplement à l’aide d’un smartphone appairé.
Des solutions de remplacement de câble comme le MUX Phoenix Contact Wireless s’appuient sur le Bluetooth pour simplifier les processus d’appairage et de connexion à un contrôleur sans configuration ni installation. Cette solution s’avère particulièrement utile dans des situations où un petit nombre de signaux numériques ou analogiques doivent être échangés entre un contrôleur et des capteurs installés sur un sous-ensemble mobile, par exemple un portique ou un bras robotisé. Une seule paire de MUX sans fil peut remplacer jusqu’à 40 câbles de signal.
Par ailleurs, la transmission radio sub-GHz est la solution privilégiée pour les connexions à faible débit de données ou à plus longue portée où une faible consommation d’énergie est impérative. Si les protocoles standard présentent des avantages comme l’interopérabilité multifournisseur, les protocoles propriétaires peuvent proposer, par exemple, une petite pile logicielle et des fonctionnalités optimisées pour une application particulière. Ainsi, les technologies sub-GHz sont capables d’assurer des connexions point à point peu coûteuses.
Les défis de l’automatisation d’usine et de processus
Lorsqu’il s’agit d’échanger des signaux de commande sur un réseau pour gérer des machines et des processus automatisés, la rapidité des échanges est essentielle. Côté filaire, la technologie de mise en réseau Ethernet sensible au temps (TSN) a été développée pour garantir des performances en temps réel avec déterminisme et un degré élevé de disponibilité. Une technologie de mise en réseau sans fil appropriée doit être capable de supporter une gestion du trafic garantissant des temps de retard déterministes avec une latence minimale. Ceci est en effet essentiel pour établir les communications rapides requises pour le contrôle de machines à grande vitesse et pour réduire à un minimum les risques de sécurité pour le personnel se trouvant à proximité.
Dans cette optique, le Wi-Fi semble être une solution appropriée. Cependant, bien que le débit de données maximal puisse prendre en charge les applications de contrôle des processus industriels, la latence et le déterminisme n’ont pas été les points forts des premières normes WLAN IEEE 802.11 destinées aux applications Wi-Fi domestiques et professionnelles. Les spécifications les plus récentes, IEEE 802.11n, 802.11ac, et les dernières spécifications IEEE 802.11ax (que l’on appelle aussi norme Wi-Fi 6) introduisent des améliorations devant notamment aider le Wi-Fi à répondre aux exigences des applications d’automatisation d’usine. Citons parmi ces améliorations une capacité et des débits de données plus élevés ainsi que plusieurs techniques telles qu’un procédé d’évaluation de canal libre (CCA) plus rapide et, en ce qui concerne le Wi-Fi 6, la réutilisation paramétrée de l’espace (PSR). Ces améliorations ont permis de réduire à un minimum la latence induite par la procédure «écouter avant de parler» (LBT) que toutes les technologies utilisant une bande de fréquence radio sans licence ont l’obligation de respecter. En conséquence, les dernières normes Wi-Fi sont bien mieux adaptées aux applications d’automatisation d’usine et de processus que celles des précédentes moutures.
Un autre problème majeur dont il faut tenir compte lorsque l’on opte pour des technologies sans fil dans un contexte industriel est le fait que cet environnement industriel contient la plupart du temps des éléments susceptibles de dégrader le débit de données, la distance de connexion et la fiabilité. Les gros objets métalliques (les machines, mais aussi des éléments de l’infrastructure du bâtiment comme des ponts ou des portes roulantes) réfléchissent les ondes radio, ce qui provoque des problèmes de réflexions par trajets multiples. De même, les murs et cloisons épais peuvent bloquer ou atténuer les signaux. Enfin, d’autres sources de signaux radio comme les équipements RFID et les réseaux Wi-Fi des bureaux à proximité peuvent causer des interférences.
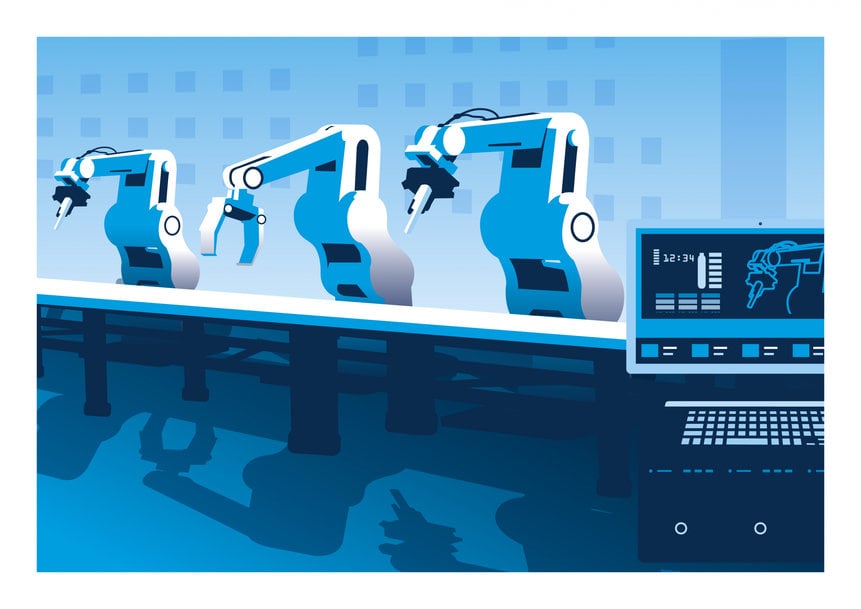
Connectivité cellulaire légère
L’émergence de l’Internet des objets (IoT) et de l’Internet des objets industriel (IIoT) a créé une demande pour connecter des appareils distants au-delà de la portée des technologies sans fil point à point à courte portée. Les technologies cellulaires et LPWAN (réseau étendu à basse consommation) pourraient bien offrir une réponse à cette demande. Initialement, les réseaux cellulaires ont été conçus pour fournir une bande passante élevée et une grande capacité de canal afin de répondre aux demandes des consommateurs mobiles. En l’état, ils s’avèrent trop coûteux et énergivores pour servir à des applications à faible débit de données.
En revanche, les technologies LPWAN comme LoRaWAN et Sigfox offrent des alternatives à longue portée.
Plus récemment, des spécifications introduites dans le cadre des normes cellulaires 4G, telles que le NB-IoT (Internet des objets à bande étroite) et le LTE-M pour la communication de machine à machine, sont mieux adaptées pour répondre aux besoins des opérateurs IoT. Cependant, ces technologies sont toujours orientées vers la connexion de capteurs distants, lesquels envoient généralement de petits paquets de données à intervalles périodiques. Ils n’offrent pas les garanties nécessaires en termes de latence et de déterminisme pour permettre de contrôler des processus à distance sur des connexions cellulaires.
Tout cela risque de changer avec l’arrivée de la 5G. Celle-ci pourrait en effet permettre à tous les objets connectés sans fil au sein de l’entreprise (Figure 1) de communiquer directement et à toutes fins avec le réseau, qu’il s’agisse d’E/S sans fil, de la mise en réseau de capteurs ou de contrôle par réseau sensible au temps (TSN).
La 5G peut-elle tout faire ?
Contrairement aux technologies de communication cellulaire précédentes, la 5G comprend des dispositions pour les communications ultra-fiables à faible latence (URLLC) et les communications massives de type machine (mMTC) qui lui permettent de satisfaire aux exigences des applications industrielles, depuis le réseau de capteurs haute densité jusqu’à l’automatisation à grande vitesse. Ces dispositions permettent aux connexions 5G de répondre aux besoins des tâches d’automatisation d’usine ou de processus. Par exemple, le contrôle de mouvement, la communication de contrôleur à contrôleur, le contrôle en boucle fermée, la communication avec des robots mobiles, la gestion des actifs de l’usine, la surveillance et la maintenance à distance ou encore la mise en réseau de capteurs à une échelle jamais atteinte auparavant. Avec sa bande passante élevée, sa faible latence et sa fiabilité, la 5G pourra même être utilisée pour des applications de réalité augmentée en soutien du personnel de production et des techniciens de service.
Une même machine ou ligne de production peut intégrer à la fois la 5G et une technologie filaire. Des dispositifs de sécurité intégrés permettent en effet de garantir la disponibilité, l’intégrité et la confidentialité. De plus, les spécifications5G fournissent les fonctionnalités nécessaires pour intégrer la 5G au TSN Ethernet filaire dans des cas d’utilisation d’automatisation industrielle.
Bien que l’organisation 3GPP soit responsable du développement des normes 5G, la 5G-ACIA est une alliance constituée dans le but de garantir que le développement permanent des normes continue de répondre aux besoins des utilisateurs industriels.
La 5G dans l’automatisation d’usine et de processus
Le 3GPP a défini quatre classes de trafic pour les cas d’utilisation d’automatisation d’usine et de processus et a déterminé les exigences de qualité de service (QoS) pour chacune d’entre elles. Les principaux paramètres de QoS sont la disponibilité du service, la fiabilité du service, la latence de bout en bout et le débit de données côté utilisateur. Les exigences secondaires comprennent la taille du message, l’intervalle de transfert, le temps de survie, la vitesse de l’équipement utilisateur, le nombre d’équipements utilisateur et la zone de service. Des exigences supplémentaires telles que la rapidité, le positionnement et la synchronisation temporelle ainsi que les exigences générales de QoS s’appliquent à tous les services de communication.
De ces quatre classes de trafic, la communication déterministe périodique est celle qui est soumise aux exigences les plus strictes. Pour cette classe, la 5G garantit une latence de bout en bout de jusqu’à 0,5 ms et une synchronicité temporelle inférieure à 1 µs pour les applications de contrôle de mouvement.
Les spécifications permettent un découpage et une isolation qui offrent aux utilisateurs la possibilité de créer plusieurs réseaux virtuels indépendants pour gérer différentes tâches de communication.
Grâce au déploiement de la 5G, les organisations sont désormais en mesure d’établir des réseaux privés, que l’on appelle aussi des réseaux non publics (NPN), qui permettent de se dispenser de services publics tels que les appels vocaux, la vidéo et la QoS du trafic Internet pour les applications industrielles. Un NPN peut être mis en œuvre en tant que réseau privé autonome installé sur le site de l’utilisateur, par exemple une usine ou un site de fabrication. Mais il est aussi possible de créer un NPN sous la forme d’un réseau virtuel hébergé sur un réseau public. La continuité des services entre les réseaux 5G non publics et publics est assurée, tout comme la prise en charge de la mobilité entre les réseaux centraux 5G et 4G.
Preuve enfin que la 5G ne saurait tarder à être utilisée pour des applications industrielles, Siemens a fait la démonstration d’un réseau 5G autonome et privé dans un environnement industriel. Ce réseau est utilisé pour tester divers aspects des performances de la 5G dans des contextes industriels, tels que la fiabilité de la communication sans fil, son comportement en temps réel et sa sécurité dans les interactions entre les humains et les machines. C’est donc sans surprise que Siemens commercialise le premier routeur industriel, le SCALANCE MUM856-1, depuis début 2021. Développé pour des applications dans des environnements industriels exigeants, ce routeur est contenu dans un boîtier IP65. Il prend en charge la 4G et la 5G et peut être utilisé aussi bien sur des réseaux de campus 5G publics que privés.
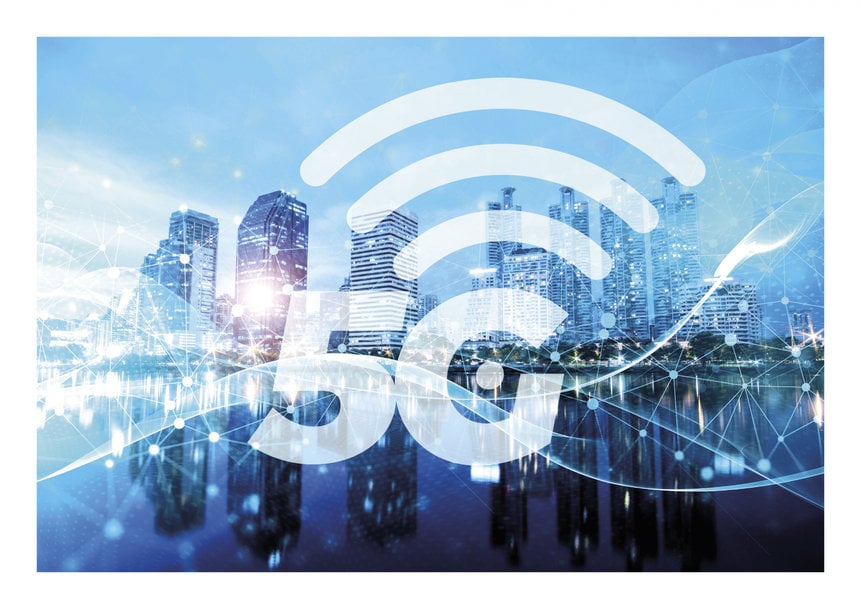
La 5G pour les déploiements à l’échelle du site
En même temps que les processus de fabrication industrielle ne cessent de devenir plus intelligents et autonomes en s’appuyant de plus en plus sur le contrôle, la gestion et la maintenance à distance, les exigences de performance imposées aux connexions sans fil ne cessent de croître. Les normes courantes et bien établies telles que le Bluetooth et le Wi-Fi ont évolué pour répondre aux besoins de fiabilité élevée, de débit élevé de données et de faible latence. D’autre part, la 5G permet désormais de se connecter directement à une grande variété d’actifs industriels tout en garantissant les performances, l’évolutivité et la fiabilité nécessaires pour traiter diverses applications, de la mise en réseau de capteurs à grande échelle jusqu’à l’automatisation à grande vitesse.
Autres ressources sur la 5G : https://resources.mouser.com/5g
www.mouser.com