electronique-news.com
08
'23
Written on Modified on
HARTING: Des circuits imprimés plats aux très petits circuits 3D implantables
L'aspect le plus remarquable de la technologie réside dans sa perpétuelle capacité d’innover et d’améliorer : des ordinateurs portables plus fins, des téléphones plus petits et des dispositifs médicaux conçus pour être discrets et à peine visibles à l'œil nu. Désormais, la plastronique remplace de plus en plus les circuits imprimés plats.
Les appareils électroniques continuent d'évoluer et de gagner en compacité grâce à la miniaturisation de leurs circuits ainsi que de leurs composants. Cette tendance a fait naître une demande accrue de composants miniatures.
La plastronique ou également appelés 3D-MID (three-dimensional mechatronic integrated devices pour dispositifs intégrés mécatroniques tridimensionnels) permet de répondre à cette attente. En effet, elle rend possible la réalisation de conceptions qui gagnent en compacité tout en améliorant leur densité fonctionnelle.
Cet article présente la plastronique ainsi que ses nombreux avantages et ses applications. Il donne également un bref aperçu de l'expertise de HARTING en la matière.
La révolution de la miniaturisation de l'électronique
Les appareils de plus petites dimensions ont un moindre impact sur l'environnement. Par exemple, un ordinateur portable présente une consommation de pointe de 60 watts, contre 175 watts pour un ordinateur de bureau. Il consomme donc 80 % de moins d'énergie que son homologue de bureau. Cette réduction significative de la consommation d'énergie est obtenue grâce à la miniaturisation.
La miniaturisation a révolutionné de nombreux secteurs : depuis le médical et la santé jusqu'à l'automobile en passant par l'électronique industrielle et grand public. Voici quelques facteurs qui explique cette tendance :
Exigences esthétiques
Nous souhaitons désormais que nos appareils soient bien conçus et visuellement attrayants.
Portabilité
Nous désirons également que nos appareils soient légers et faciles à transporter.
Baisse des coûts
Si la miniaturisation peut être initialement coûteuse, elle permet néanmoins l'utilisation de moins de et à long terme de réaliser des économies. Ce qui peut conduire à réaliser des économies à long terme.
Réduction de la consommation d'énergie et respect de l'environnement
Les composants de plus petites dimensions consomment moins d'énergie. Ce qui permet de réduire les coûts d'exploitation, d'augmenter la durée de vie des piles et de promouvoir des produits plus écologiques.
Moindre dissipation de chaleur
Comme les petits composants consomment moins d'énergie, les appareils électroniques génèrent moins de chaleur. Les dissipateurs thermiques ou les ventilateurs encombrants peuvent donc être supprimés. Ce qui réduit le poids, le coût, la puissance et le bruit des appareils.
L’industrie at tendance à augmenter la densité fonctionnelle de ses appareils. Les composants doivent donc être de plus en plus petits et interconnectés.
La plastronique permet de répondre à ces exigences en allégeant la masse des produits et en optimisant leur encombrement tout en leur permettant d'offrir des performances identiques voire supérieures.
Qu'est-ce que la technologie 3D-MID ?
Le terme "mécatronique", qui associe les mots "Méca" (mécanique) et "Tronique" (électronique), a été inventé en 1969 par un ingénieur senior de la société japonaise Yaskawa.
Depuis lors, la définition a évolué. Elle est désormais utilisée pour décrire l'utilisation conjointe de technologies numériques, électroniques et mécaniques pour concevoir des systèmes plus intelligents, tels que des solutions robotiques, de contrôle et électromécaniques.
La technologie 3D-Circuits de HARTING permet d'intégrer directement les pièces 3D-MID ou la pièce thermoplastique moulée par injection aux circuits et composants électroniques. Ceci permet de gagner en compacité et en densité fonctionnelle. Imaginez un circuit imprimé nettement plus compact et constitué de plastique plutôt que de métal.
En outre, les circuits imprimés moulés par injection réduisent considérablement le nombre d'étapes de fabrication, les temps d'assemblage, le nombre de composants nécessaire, et donc les coûts de production.
Comment fonctionne la plastronique ?
La flexibilité de la technologie 3D-MID offre davantage de liberté aux concepteurs. L'intégration de fonctions électriques et mécaniques dans un composant tridimensionnel offre des infinies.
Les concepteurs définissent leurs exigences ainsi que des spécifications dimensionnelles très précises. Les composants sont ensuite moulés par injection.
Le moulage par injection consiste à chauffer et à faire fondre des matériaux tels que le plastique puis de les injecter dans un moule et de les refroidir pour obtenir la forme souhaitée. C'est un procédé couramment utilisé dans de nombreuses industries car il permet de produire rapidement et en volume des pièces de forme complexe.
La flexibilité moulage par injection permet aux concepteurs d'y avoir recours pour fabriquer pratiquement n'importe quelle pièce en respectant les spécifications requises. Avant de réaliser un moule, différentes techniques de simulation permettent de vérifier si les pièces répondent bien aux exigences et des échantillons de pièces peuvent être fabriqués en prototypage rapide.
Vient ensuite la phase d'activation par laser grâce à la technologie LDS (laser-direct structuring), un procédé développé en 1996 par LPKF Laser & Electronics. Un faisceau laser grave directement la piste conductrice sur la pièce plastique moulé par injection.
Le matériau plastique utilisé pour le moulage par injection contient en effet des additifs spécifiques que les faisceaux laser pourront activer. Les lasers révèlent les zones où les structures conductrices seront situées.
Dans le processus de placage chimique, le cuivre ne se dépose que sur les zones structurées par le laser. Cela permet aux ingénieurs de créer des circuits électroniques très précis.
Lors de la métallisation ultérieure dans un bain de cuivre, des traces conductrices se forment dans les zones qui ont ainsi été activées et permettront aux métaux d'y adhérer.
La combinaison de composants mécaniques et électriques permet de concevoir et de fabriquer plus facilement et à moindre coût des dispositifs électroniques aux fonctionnalités complexes. Cela offre de nouvelles opportunités de conception et peut permettre aux fabricants ainsi qu'aux consommateurs de réaliser des économies significatives.
Quels sont les avantages et les applications de la plastronique ?
- Intégration de fonctions mécaniques et électriques dans un seul composant
- Amélioration de la fiabilité et de la qualité
- Flexibilité qui permet des options de conception illimitées
- Diminution la taille et le poids
- Réduction du temps d'assemblage et donc des coûts de fabrication.
Applications 3D-MID
Qu'il s'agisse d'appareils destinés au marché médical ou de l'automobile ou de gadgets pour le grand public, pratiquement tous les équipements techniques actuels et futurs sont conçus et seront des matières plastiques et intégreront de l'électronique.
La plastronique peut transformer la manière de concevoir des produits tels que :
- les capteurs et les boîtiers électroniques miniaturisés
- les supports de LED et les modules d'éclairage
- les antennes et les modules de connectivité
Presque toutes les industries peuvent tirer parti d'une manière ou d'une autre des circuits 3D. De nombreux secteurs, tel que le domaine médical, ont notamment des besoins importants en termes de miniaturisation.
La plastronique appliquée au médical
La mécatronique est une discipline prometteuse qui profite à de nombreuses industries, telles que le médical ou la santé.
Des progrès en matière de diagnostic et de traitement ont été rendus possibles grâce à la miniaturisation de l'électronique qui elle-même a bénéficiée des avancées importantes de la technologie 3D-MID.
Imaginez que vous deviez subir une endoscopie. La plupart des gens sont mal à l'aise à l'idée de vivre une expérience qui consiste à faire pénétrer un long tube fin muni d’une petite caméra dans le corps.
Heureusement, grâce à la technologie 3D-MID, les fabricants peuvent désormais concevoir des dispositifs moins invasifs et plus confortables pour les patients, notamment lorsqu'il s'agit de surveiller et d'examiner l'intérieur d'un organe ou d'une cavité du corps.
Il n'est plus nécessaire d'insérer dans la gorge un long endoscope équipé d'une petite caméra. A la place, vous avalez une capsule non invasive comme vous le feriez en prenant vos vitamines.
Cette capsule renferme une petite caméra endoscopique qui transmet à votre médecin des images de votre corps sur 360 degrés. Ceci permet de visualiser votre tube digestif sans avoir à recourir à des procédures invasives.
Ceci n’est qu’exemple parmi d’autres du progrès technologique qui rend plus agréable une situation auparavant inconfortable.
La mécatronique est également utilisée pour concevoir de nouveaux types de prothèses, telle que la prothèse de bras Luke Arm, contrôlée par la pensée qui permet aux patients ayant perdu un membre d'effectuer des tâches quotidiennes.
Les technologies 3D-MID sont également utilisées pour concevoir de petits appareils médicaux tels que des prothèses auditives, des implants ainsi que des dispositifs chirurgicaux et dentaires. Les circuits imprimés 3D de toutes les dimensions peuvent être fabriqués tout en conservant les mêmes fonctionnalités et en respectant les mêmes normes de sécurité.
Conclusion
Les possibilités offertes par la plastronique sont sans limite. Au fur et à mesure que cette technologie progresse, nous nous attendons à ce que de plus en plus d’entreprises les intégreront dans leurs projets d'économie d'espace, réduisant ainsi les procédures d'assemblage et les coûts.
URL
www.3D-Circuits.com
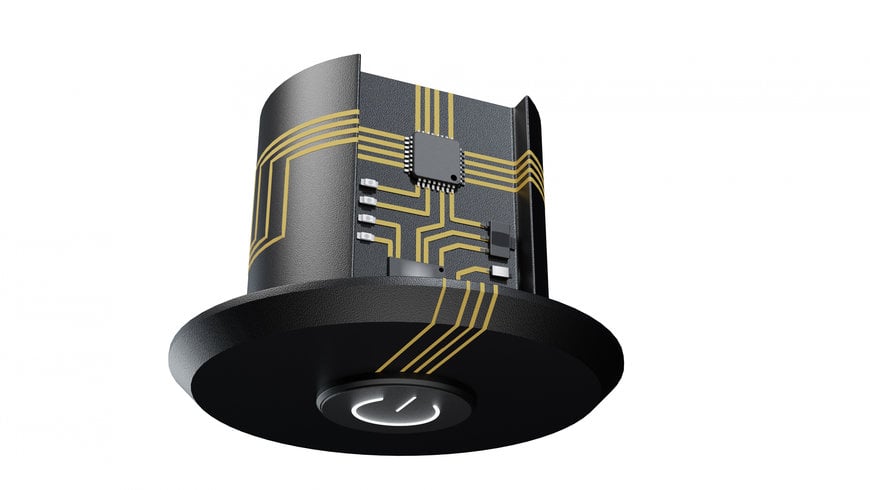
Appareil auditif :
L'intégration de fonctions et le routage tridimensionnel des pistes du circuit permettent d'optimiser l'encombrement de l'électronique des appareils auditifs.
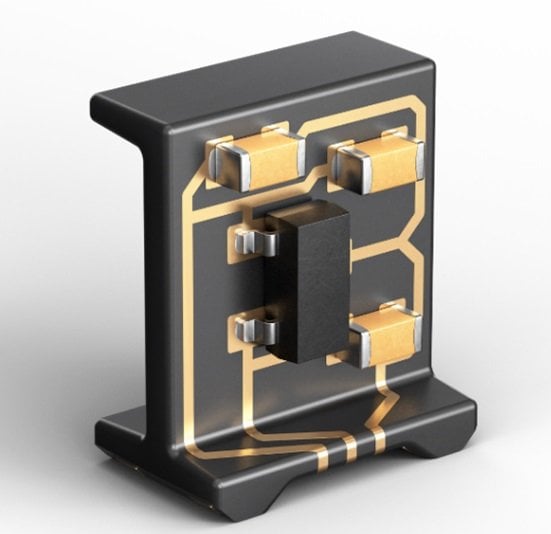
Support de composants :
Le support de composants 3D-MID a été développé par HARTING. Il sert d'interface de connexion entre un circuit imprimé (PCB) et les composants électroniques (tels que les LED, les circuits intégrés, les photodiodes ou les capteurs).
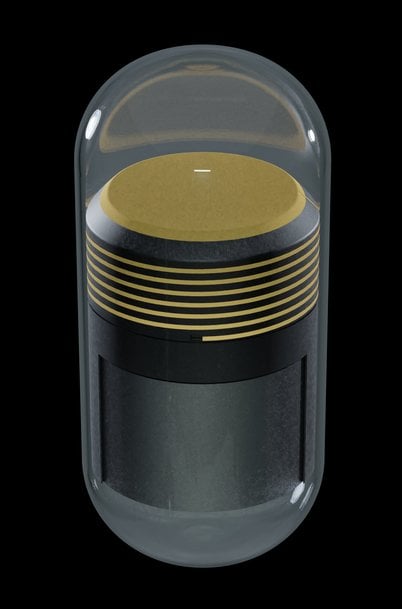
Antenne encapsulée :
Elle s'avale comme une pilule. Cette solution confortable remplace l’utilisation d’un endoscope.